How UTOC works
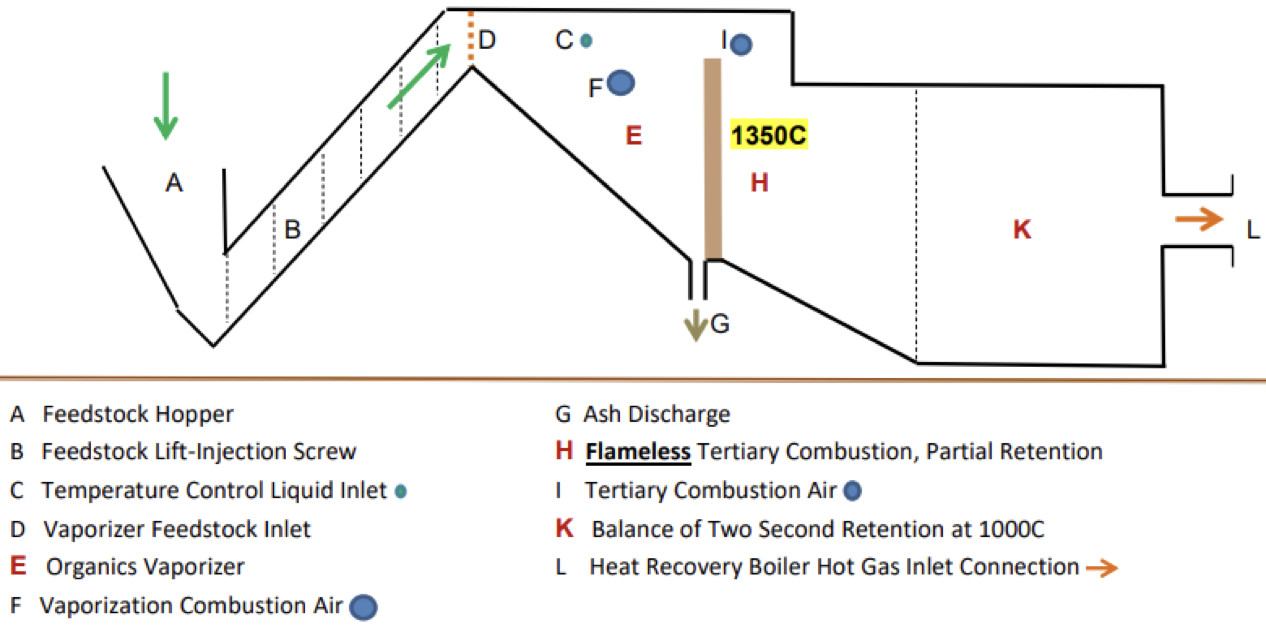
When people come to see the UTOC in action at our demonstration site, the features they first notice is the system is quiet, there's no smoke and the only fuel it needs is garbage. One of our guests, after watching it for a while, asked when we were going to start it up to which we replied, "it's been running since you arrived."
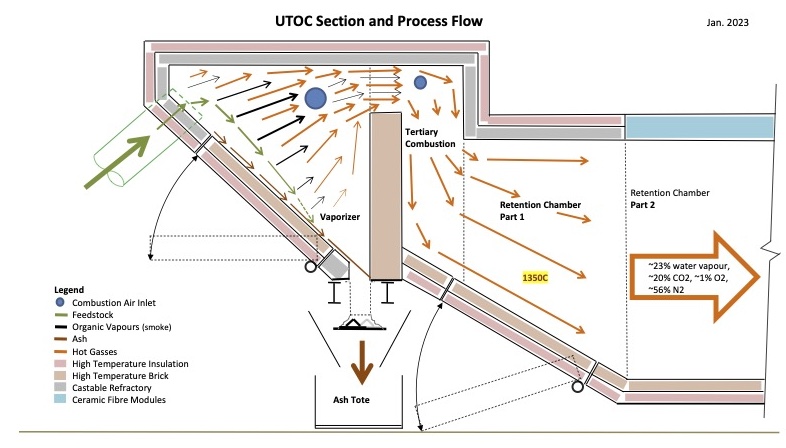
The Vaporizer
The diagram above shows the three chambers of the UTOC. The first chamber is the vaporizer where organic waste, either shredded solids, liquids or gases, enters via the feedstock auger or liquid/gas injection port. UTOC is designed to run 24/7, but when we first start it up we use propane for the first 24 hours to heat this chamber. After startup, the UTOC requires no fuel other than the garbage itself. The fireball above the sloped surface radiates heat, up to 1,350°C, onto feedstock slowly flowing down the slope vaporizing organic waste into smoke and ash. The resulting smoke burns as clean as natural gas, so we inject just enough oxygen to burn up to 90% of the smoke, regulating the vaporizer temperature .
Vaporizer temperature is automatically regulated and will change according to the energy content of the incoming material; if the material is highly volatile like oil, lower temperatures are needed than if the material is less volatile like wet garbage. To prevent the chamber exceeding 1,350°C, we inject waste liquids (shown as "Temperature Control Liquids" in the infographic) to cool it down.
Already in this first chamber, the organic waste is vaporized into smoke of which 90% is combusted while the remaining inorganic fraction is turned to sterile ash as it slides down the slope towards the ash tote.
The Tertiary Chamber
The remaining 10% of the smoke now enters the next chamber which burns at a constant 1,350°C with just a little more oxygen than is needed to ensure the smoke is completely burned. All the smoke is now completely combusted leaving only clean hot gases with unprecedentedly low emissions that, so far as third party testing shows, require no further cleaning to meet regulatory emission limits.
The Retention Chamber
We've consulted with the Canadian Food Inspection Agency in creating the UTOC. To maximize the destruction of pathogens, like the BSE prion, the most difficult to destroy ("mad cow disease"), they require that gases be held at 850°C for two seconds. That's the only function of the retention chamber which ranges between 900°C and 1,320°C, exceeding CFIA requirements.